摘 要:本文介紹了國內首例ACES裝置高壓甲銨冷凝器雙相不銹鋼換熱列管的管子-管板角焊縫大規模修復案例,結合具體的修復實(shí)施過(guò)程,指出修復重點(diǎn)環(huán)節的技術(shù)要求。
關(guān)鍵詞:高壓甲銨冷凝器 管子-管板角焊縫 雙相不銹鋼焊接
前言
陜西渭河重化工有限責任公司尿素裝置,采用日本東洋工程公司(Toyo Engineering Co.)ACES工藝流程,于1997年建成投入運行至今。
高壓設備中,甲銨冷凝器為固定管板式換熱器,兩臺立式并聯(lián)(位號分別為EA101/102),內部耐蝕材料為DP-12型雙相不銹鋼,制造焊接材料為SUS329型雙相不銹鋼。
經(jīng)過(guò)長(cháng)期使用后,其管子-管板角焊縫出現大面積腐蝕缺陷,局部已經(jīng)存在泄漏征兆,嚴重威脅到設備的安全運行。并且,國外同樣設備已經(jīng)出現了因管子-管板角焊縫腐蝕造成的嚴重泄漏事故。
2009年3月,在渭化公司統一安排下,重慶奧林特機電技術(shù)有限公司調配專(zhuān)業(yè)力量,對兩臺設備上管箱內的全部管子-管板角焊縫,進(jìn)行了徹底的修復處理。
現將修復過(guò)程及相關(guān)技術(shù)心得,簡(jiǎn)要介紹如下。
1 設備概況
1.1 設備技術(shù)特性
高壓甲銨冷凝器主要設備技術(shù)特性如表1、表2。
表1 EA101主要設備技術(shù)特性
介質(zhì)
參數 |
殼 側 |
管 側 |
蒸汽 |
NH3 /CO2/甲銨液 |
設計壓力MPa |
0.8 |
18 |
操作壓力MPa |
0.49 |
17.1 |
設計溫度℃ |
200 |
220 |
操作溫度℃ |
158/158 |
183/176 |
材 質(zhì) |
SA516M Gr.485 |
DP-12 |
列管規格 |
¢19×2×10300 |
2820根 |
表2 EA102主要設備技術(shù)特性
介質(zhì)
參數 |
殼 側 |
管 側 |
蒸汽 |
NH3 /CO2/甲銨液 |
設計壓力MPa |
2.1 |
18 |
操作壓力MPa |
1.72 |
17.1 |
設計溫度℃ |
190 |
220 |
操作溫度℃ |
137/155 |
183/176 |
材 質(zhì) |
SA240 316L-VG |
DP-12 |
列管規格 |
¢19×2×10300 |
1735根 |
換熱管材料牌號為SA240/NAR DP-12,其化學(xué)成分見(jiàn)表3。
表3 DP-12化學(xué)成分
C |
Si |
Mn |
P |
0.03 |
0.75 |
1.1 |
0.03 |
S |
Cr |
Ni |
Mo |
0.03 |
24.8~26 |
6.5~7.5 |
2.5~3.2 |
Cu |
N |
W |
|
0.2~0.4 |
0.1~0.3 |
0.1~0.3 |
1.2 設備腐蝕形貌
2008年大修時(shí)檢查發(fā)現:管子-管板角焊縫存在嚴重的復相晶間腐蝕,和2007年相比,腐蝕加劇趨勢明顯。
具體表征為:表層金屬組織大面積疏松脫落、收弧點(diǎn)發(fā)黑潰爛、焊肉局部穿孔。
腐蝕形貌見(jiàn)圖片1、圖片2、圖片3。
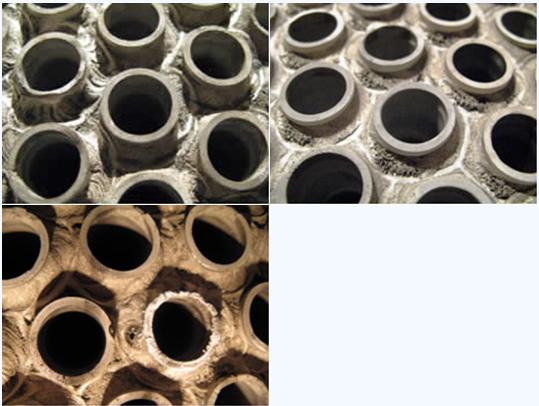
2 修復技術(shù)準備
2.1 修復思路的確定
1)修復范圍:
針對設備實(shí)際腐蝕現狀,參考國外相同設備的泄漏事故,本著(zhù)預防性的原則,決定將兩臺設備上管箱內的全部管子-管板角焊縫進(jìn)行修復。
2)原管子-管板角焊縫焊肉的清除:
由于腐蝕因素,原有制造形成的表層焊肉已經(jīng)不再是穩定的奧氏體-鐵素體雙相組織;若直接在上面補焊,則一定時(shí)間后,表層金屬一旦腐蝕,將直接面臨新的泄漏危險。
因此,我們確定了先將舊焊縫表層焊肉徹底清除,再重新焊接的修復原則。
3)焊接方式:
由于現場(chǎng)修復與實(shí)際制造的工況差別,因此,不考慮使用管子-管板自動(dòng)焊,而是采用傳統的手工鎢極氬弧焊。
4)焊接材料:
根據腐蝕試樣的試驗結果,采用25-22-2型純奧氏體焊絲和DP-3型雙相鋼焊絲,均可滿(mǎn)足耐蝕性能要求;其中,25-22-2材料與DP-12材料進(jìn)行異種鋼焊接獲得的焊縫組織更加穩定,焊接質(zhì)量容易控制。
但,在日本東洋工程公司的強烈堅持下,由于其有成熟的焊接工藝評定等原因,最終確定采用DP-3型雙相鋼焊絲。
其牌號為SUS329J4L DP-3T(UNS S39226),化學(xué)成分見(jiàn)表4。
表4 DP-3T化學(xué)成分
C |
Si |
Mn |
Ni |
Cr |
0.01 |
0.37 |
0.78 |
9.3 |
25.3 |
Mo |
Cu |
W |
N |
|
3.03 |
0.4 |
0.27 |
0.17 |
|
2.2 焊肉清除機具的選擇
由于雙相鋼本身硬度較高,腐蝕后其表面產(chǎn)物相當硬脆,普通的打磨方式無(wú)法進(jìn)行有效清除,必須采用機械切削。
經(jīng)對比試驗,我們最終選擇了日立造船出產(chǎn)的氣動(dòng)式管端加工機。
其優(yōu)點(diǎn)在于:利用換熱管內壁定心,簡(jiǎn)便可靠;內置式氣動(dòng)馬達,無(wú)級調速,可任意變換切削速度以控制切削力大小;合金刀片雙面對稱(chēng)安裝,可計數進(jìn)刀量控制,能有效保證加工精度。
2.3焊接器具及背保護工裝的準備
1)焊接器具:
為了從施工器具的角度保障焊接可靠,我們選擇了ESAB LTN-250A焊機,氣冷式焊炬內置周向濾網(wǎng)以保證氣流穩定性,噴嘴直徑¢10,鎢極直徑¢2。
2)背保護工裝:
為避免列管內壁熱影響區氧化,焊接時(shí)管內應通氬實(shí)現被保護。
我們專(zhuān)門(mén)設計制作了背保護工裝,通氬氣的嘴子內裝有不銹鋼絲網(wǎng),可使通道截面積盡量增大,使氬氣從保護嘴送出分布在所有焊接時(shí)有可能達到400℃以上的管壁區域,并由列管頂端逸出。
2.4焊接工藝評定及焊工考試
1)焊接工藝評定:
由東洋工程公司提供原始制造使用的焊接工藝評定供參考。
實(shí)際使用時(shí),和原始工藝評定相比,主要存在以下不同:
①焊接層數不同。
本次修復焊接不存在原始制造時(shí)的打底層;
②焊接材料不同。
本次焊接使用的DP-3T焊絲,為原始制造時(shí)使用焊絲的改良型。
③焊接規范的修正:
在東洋工程公司提供焊接工藝評定的基礎上,出于減小修復焊接過(guò)程對換熱管原內壁熱影響區熱輸入量的考慮,我們建議對焊接規范進(jìn)行了以下修正,并得到了東洋工程公司的認可。
主要調整了焊絲直徑,減小了焊接電流,控制管壁熔深及管內壁熱影響區顏色更為嚴格,
2)焊工考試:
采用東洋工程公司提供的考試試件進(jìn)行。
鋼板(模擬管板耐蝕層)厚度為30mm,材料為DP-12型;換熱管材料、規格與設備內實(shí)際相同;焊絲采用DP-3T ¢1.2/1.6,共焊接兩層。
按與實(shí)際狀況相同的列管間距、管端伸出高度進(jìn)行試件的加工、組裝。
焊接完畢后,由奧林特公司現場(chǎng)技術(shù)負責人會(huì )同日方技術(shù)代表共同進(jìn)行以下項目的考核驗收:
①宏觀(guān)檢查焊縫、管橋三角區外觀(guān)成型及管端完整性;
②對焊縫及管橋三角區進(jìn)行PT檢測;
③將試件剖開(kāi),對斷面進(jìn)行宏觀(guān)檢查,重點(diǎn)是管壁熔深及換熱管外壁與管板結合根部熔合狀況;
④對斷面進(jìn)行金相檢查。
共8名焊工,每人焊接1塊試件計20根換熱管。
考試結果為:7人一次合格,1人經(jīng)再培訓后合格。
2.5 修復過(guò)程主要質(zhì)量控制點(diǎn)的建立
為確保修復質(zhì)量,建立控制點(diǎn)如表5,并組成專(zhuān)門(mén)質(zhì)量檢查組,按規定時(shí)間表進(jìn)行檢查控制。
表5 修復質(zhì)量控制點(diǎn)明細
檢查項目 |
檢查內容摘要 |
檢查類(lèi)別 |
機械加工 |
加工位置、加工尺寸 |
W |
第一層
焊接 |
焊接參數、焊接材料 |
W |
焊縫成形、焊肉表面氣孔、焊縫收弧縮孔、管壁熔深、管板三角區凹陷及是否存在漏焊 |
H |
PT檢測 |
H |
第二層
焊接 |
焊接開(kāi)始前確認:
缺陷已經(jīng)全部返修、全部PT檢測合格、無(wú)漏焊 |
H |
焊接參數、焊接材料 |
W |
焊縫成形、焊縫腰高、焊肉表面氣孔、焊縫收弧縮孔、管壁熔深、管板三角區凹陷及是否存在漏焊 |
H |
PT檢測 |
H |
交付氨滲漏前確認:
缺陷已經(jīng)全部返修、全部PT檢測合格、無(wú)漏焊 |
H |
氨滲漏試驗 |
殼側氨滲漏 |
H |
壓力試驗 |
管程氣壓試驗 |
H |
說(shuō)明:W為現場(chǎng)確認,H為檢查停止點(diǎn)。
3 修復過(guò)程重點(diǎn)環(huán)節及質(zhì)量要求
3.1 機械加工
清除原焊縫表層焊肉,并形成新的焊接坡口。
1)幾何尺寸:
按圖1所示。
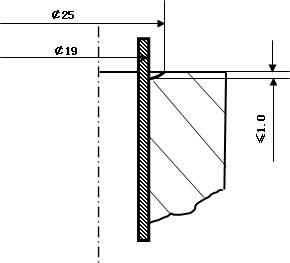
2)外觀(guān)質(zhì)量:
管外壁無(wú)加工損傷;加工面寬窄均勻,管橋三角區無(wú)明顯凸起;加工面無(wú)明顯腐蝕產(chǎn)物殘留。
3.2第一層焊接
1)焊接參數:
焊接電流 |
外側保護氣 |
內側保護氣 |
焊絲直徑 |
70-80A |
10~15L/min |
5~10L/min |
¢1.2 |
2)操作要求:
①瞄準鎢極位置角度大約10°,絕對避免將鎢極朝向管外側。見(jiàn)圖2所示。
②采用高頻,在管板起弧,從焊接部位外側送入焊絲,控制管壁熔深在0.3~0.8mm,最大不得超過(guò)1.0mm。
③管子外壁與管板的結合根部必須焊透,送絲量要保持足夠以免焊縫凹陷;
④收弧采取延時(shí)冷卻;最終收弧點(diǎn)處理方式為重熔或部分打磨,收弧部位要比其它焊接部位高出1.0mm左右。
⑤鎢極尖磨損后要及時(shí)更換。
⑥為了防止溫度上升,不要連續焊接相鄰的管子;采取分道間斷焊接,每根列管角焊縫分三次焊完,即逆時(shí)針?lè )较蛎看魏?20度角。
3)焊縫外觀(guān)成形及尺寸:
按圖4所示進(jìn)行控制。
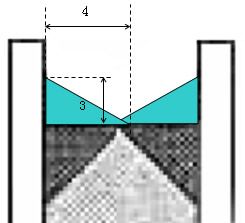
4)宏觀(guān)檢查:
①焊縫成形:按圖4要求,不允許凹陷部位的存在。
②外觀(guān)缺陷:不允許任何的焊肉表面氣孔、焊縫收弧縮孔、咬邊、裂紋、焊肉過(guò)大。
③內壁熱影響區:顏色只能為正常的銀色或金黃色,允許局部淺藍色存在,不得存在深藍色及內壁燒穿現象。
④換熱管端:除由于管端已經(jīng)存在的原腐蝕減薄及缺口而造成的塌焊以外,不得允許管端熔化現象的存在。
5)滲透探傷:
①焊接后冷卻到40℃進(jìn)行;
②不允許有任何線(xiàn)性及孔型缺陷的存在;凡發(fā)現前述類(lèi)型缺陷,必須返修;
③探傷確認完后清理表面,用脫鹽水沖洗+鋼絲刷清理方式,除去表面殘留的顯像劑,以免影響下一層焊接質(zhì)量。
6)焊縫返修:
①過(guò)程返修:焊接過(guò)程中,焊工自行發(fā)現的缺陷,可按返修技術(shù)作業(yè)程序自行進(jìn)行。
②通知返修:宏觀(guān)檢查及滲透探傷發(fā)現的缺陷,在接到返修通知后進(jìn)行。
③返修技術(shù)作業(yè)程序:焊接冷卻到40℃后,用筆式砂輪打磨消除缺陷,再按焊接要求對返修部位進(jìn)行補焊;補焊部位焊肉要比其它焊接部位高出1.0mm左右。
④返修后質(zhì)量確認:除進(jìn)行宏觀(guān)檢查確認外,還必須進(jìn)行二次滲透探傷。
3.3第二層焊接
1)焊接參數:
焊接電流 |
外側保護氣 |
內側保護氣 |
焊絲直徑 |
80-90A |
10~15L/min |
5~10L/min |
¢1.6 |
2)操作要求:
與第一層焊接相同。
3)焊縫外觀(guān)成形及尺寸:
按圖5所示進(jìn)行控制。
4)管橋三角區成形:
管橋三角區不得形成凹坑,焊接時(shí)必須補平。見(jiàn)圖6所示。
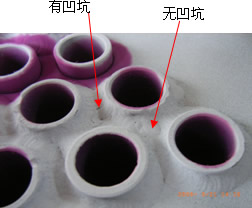
5)宏觀(guān)檢查:
除焊縫成形及官橋三角區外觀(guān)按圖5、圖6所示要求進(jìn)行檢查外,其余檢查要求與第一層焊接相同。
6)滲透探傷:
與第一層焊接相同。
7)焊縫返修:
與第一層焊接相同。
3.4最終檢驗確認:
由于現場(chǎng)不具備在氨滲漏試驗之前進(jìn)行水壓試驗的條件,故最終檢驗確認手段為氨滲漏試驗+管程氣壓試驗。
1)氨滲漏試驗:
按HG/T 3176-2002《尿素高壓設備氨滲漏試驗方法》規定,進(jìn)行殼側氨滲漏試驗。
2)管程氣壓試驗:
結合系統開(kāi)車(chē)升壓過(guò)程進(jìn)行,壓力至操作規定值。
4 修復質(zhì)量檢驗結果
4.1 第一層焊接
1)宏觀(guān)檢查后返修率3%,主要返修原因在于氣孔的處理;
2)PT檢測后返修率1%,主要返修原因仍然是氣孔的處理。
4.2 第二層焊接
1)宏觀(guān)檢查后返修率0.5%,主要返修原因在于官橋三角區凹陷;
2)PT檢測后無(wú)返修。
4.3 氨滲漏試驗
一次合格。
4.4 管程氣壓試驗
一次合格。
4.5 遺留問(wèn)題
1)原內件支撐螺柱附近,共約0.5%的換熱列管,管端被電弧熔塌形成小缺口,但缺口底部均高于焊縫,故不再處理。
2)管板邊緣部位,共約0.3%的換熱列管,靠管箱筒體側,內壁熱影響區顏色發(fā)藍,保留觀(guān)察。
5 運行一年后實(shí)際效果
2010年3月,我們對兩臺設備修復焊接部位,進(jìn)行了全面的腐蝕檢查。
檢查結果發(fā)現:全部修復焊縫表面鈍化良好,金屬光澤明顯,不存在異常腐蝕缺陷;原遺留的局部管內壁發(fā)藍處,無(wú)疏松條帶存在;原遺留的局部管端熔化形成缺口處,無(wú)腐蝕溝槽形成。
實(shí)際腐蝕形貌見(jiàn)圖片4、圖片5。
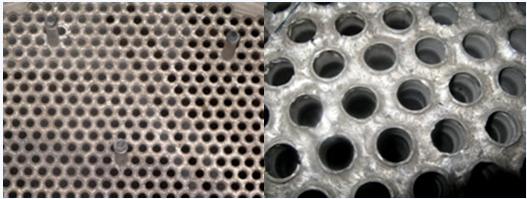
6 結束語(yǔ)
1)雙相鋼焊縫腐蝕產(chǎn)物的清理,采用機械切削方式最為有效快捷;
2)焊接方案的制訂、焊工的技能培訓、焊接工藝紀律的執行、焊接檢驗控制點(diǎn)的確立,是保障修復施工質(zhì)量的基礎;
3)在管子-管板角焊縫的修復焊接過(guò)程中,控制管壁熔深是關(guān)鍵,焊接氣孔的處理是難點(diǎn)。
作者簡(jiǎn)介:余竹君,男,42歲,1988年畢業(yè)于重慶大學(xué)機械工程系,高級工程師,重慶奧林特機電技術(shù)有限公司副總經(jīng)理。長(cháng)期從事尿素高壓設備腐蝕監測與維修的技術(shù)管理,先后參加過(guò)尿素高壓設備的腐蝕行為研究、耐蝕材料國產(chǎn)化研制、修復技術(shù)開(kāi)發(fā)及應用等多項國際國內合作課題。