摘 要:本文介紹了渦流檢測技術(shù)原理及主要特點(diǎn),提出在役換熱器換熱列管的檢測實(shí)施要點(diǎn),并就該技術(shù)在合成氨裝置中的實(shí)際檢測應用作簡(jiǎn)要介紹。
關(guān)鍵詞:換熱列管 渦流檢測
0 前 言
在合成氨生產(chǎn)裝置中,廣泛使用著(zhù)各種形式的列管式熱交換器,其中有不少換熱器在高溫、高壓及腐蝕介質(zhì)中運行。由于介質(zhì)腐蝕、沖刷、疲勞應力等作用,會(huì )使列管管壁產(chǎn)生各種腐蝕缺陷、損傷和壁厚減薄,這將嚴重威脅設備的安全運行。
而由于設備結構的特殊性或系統裝置條件的不具備,很多換熱器不能進(jìn)行常規的殼側水壓或氣壓試驗,無(wú)法準確查找出換熱管的泄漏部位,更不能對換熱列管可能存在的隱患作出有效的預報性診斷。
因此,采用渦流檢測技術(shù)對這些在役換熱器的換熱列管進(jìn)行定期檢測,掌握列管缺陷的存在及發(fā)展情況,掌握列管最小壁厚值的變化情況,從而對換熱列管使用狀況作出有效的預防性診斷及處理,是保證裝置生產(chǎn)設備長(cháng)周期安全運行的可靠技術(shù)手段。
1 渦流檢測技術(shù)原理
渦流檢測技術(shù)的理論基礎是電磁感應。
載有交變電流的檢測線(xiàn)圈靠近導電試件時(shí),由于激勵線(xiàn)圈磁場(chǎng)的作用,將會(huì )在試件中感應出渦流(見(jiàn)圖1);而渦流的大小、相位及流動(dòng)形式受到試件導電性能的影響,同時(shí)產(chǎn)生的渦流也會(huì )形成一個(gè)磁場(chǎng),這個(gè)磁場(chǎng)反過(guò)來(lái)又會(huì )使檢測線(xiàn)圈的阻抗發(fā)生變化。
通過(guò)測定檢測線(xiàn)圈阻抗的變化,就可以判斷出被測試件的性能及有無(wú)缺陷。
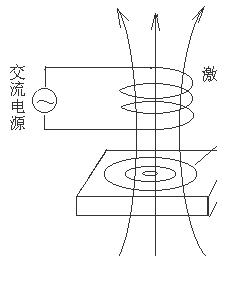
圖1 渦流檢測的原理
對在役換熱列管的渦流檢測,采用內穿過(guò)式線(xiàn)圈作為“檢測探頭”,通常由兩個(gè)或兩個(gè)以上的測量線(xiàn)圈組成。
對列管進(jìn)行渦流檢測時(shí),線(xiàn)圈中加載的交變電流將在列管壁上形成渦流場(chǎng)(見(jiàn)圖2);而列管的幾何缺陷、電磁異常和壁厚變化等因素都將對該渦流場(chǎng)形成影響。
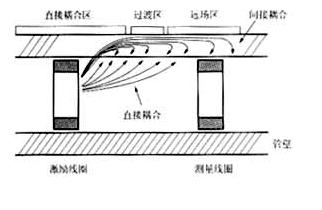
圖2 列管渦流場(chǎng)形成示意圖
當列管無(wú)影響渦流場(chǎng)的因素存在時(shí),渦流場(chǎng)無(wú)變化,兩個(gè)測量線(xiàn)圈反向連接感應電壓為平衡狀態(tài),沒(méi)有輸出;當列管存在影響渦流場(chǎng)的因素時(shí),渦流場(chǎng)的變化又使測量線(xiàn)圈的阻抗和感生電壓發(fā)生改變。
測出阻抗變化量,經(jīng)過(guò)儀器處理可判列管的缺陷情況——渦流探傷;
測出感生電壓變化量,就可得出列管壁厚的變化狀況——渦流測厚。
2 渦流檢測技術(shù)類(lèi)型
渦流檢測技術(shù)手段分為兩大類(lèi)型:常規渦流檢測和遠場(chǎng)渦流檢測。
2.1 常規渦流檢測
適用于純奧氏體不銹鋼、純鈦及其合金、純鎳及其合金、銅、鋁等非鐵磁性材料。
常規渦流場(chǎng)形成于“近場(chǎng)區”,其渦流信號具有趨膚效應及在深度方向的相位滯后效應。
利用相位滯后效應,在檢測參數合適的前提下,通過(guò)建立對比試樣管上不同深度人工模擬缺陷的阻抗圖及缺陷深度—相位圖(見(jiàn)圖3、圖4),可在渦流探傷時(shí)有效區分列管壁缺陷的性質(zhì)及類(lèi)型。
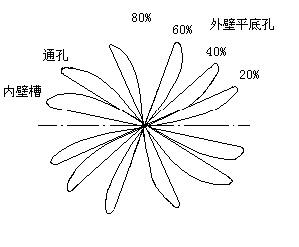
圖3 常規渦流缺陷阻抗圖
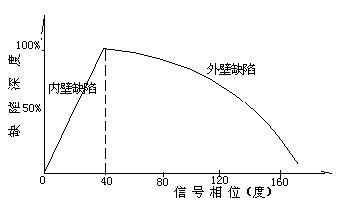
圖4 常規渦流缺陷深度—相位曲線(xiàn)圖
2.2 遠場(chǎng)渦流檢測
遠場(chǎng)渦流技術(shù)基于一種特殊物理現象——遠場(chǎng)渦流效應,是一種能穿透金屬管壁的低頻渦流檢測技術(shù)。
特別適用于奧氏體-鐵素體雙相不銹鋼、鐵素體不銹鋼、Cr-Mo鋼、碳鋼等鐵磁性材料。
檢測換熱列管時(shí),內置式探頭置于被檢測管內,探頭上有一個(gè)激勵線(xiàn)圈,還有一個(gè)(或二個(gè))測量線(xiàn)圈;激勵線(xiàn)圈和測量線(xiàn)圈的距離為列管內徑的2-3倍。
激勵線(xiàn)圈通以低頻交流電,發(fā)出的磁力線(xiàn)(能量)穿過(guò)管壁向外擴散,在遠場(chǎng)區又再次穿過(guò)有表面缺陷的管壁向內擴散,被測量線(xiàn)圈接收(見(jiàn)圖5)。
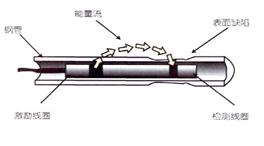
圖5 遠場(chǎng)渦流場(chǎng)能量傳遞示意
若管子壁厚為h,則磁場(chǎng)兩次穿過(guò)管壁造成的振幅衰減和相位滯后由下式?jīng)Q定
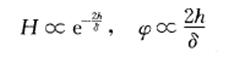
H—磁場(chǎng)強度振幅衰減值
δ—集膚深度
φ—測量線(xiàn)圈感應電壓和激勵電流間的相位滯后值
由上式可見(jiàn):若管壁存在裂紋、凹坑及腐蝕等缺陷,則相應部位管壁厚度減小,導致檢測信號相位滯后值減小,振幅衰減值增大。
據此,可以根據檢測信號相位及幅值的變化,判斷被檢測換熱管缺陷狀況。
2.3 遠場(chǎng)渦流和常規渦流技術(shù)的比較
1)測量磁場(chǎng)區域:
常規渦流線(xiàn)圈置于直接耦合區,測量的是傳播到管壁又直接返回的磁場(chǎng)。
遠場(chǎng)渦流為避免直接磁耦合,測量線(xiàn)圈必須置于遠離激勵線(xiàn)圈的間接耦合區,測量穿過(guò)管壁后在管外沿管軸傳播一段距離返回管內的磁場(chǎng)。
因此,遠場(chǎng)渦流檢測獨具有透壁性,能檢測整個(gè)管壁上的缺陷而不受集膚效應的限制,克服了電導率和磁導率的影響,對內外壁的缺陷具有相同的靈敏度,且相位信號不受提離效應的影響。同時(shí),對填充系數要求低,對探頭在管內行走產(chǎn)生的偏心影響很小。
2)檢測頻率:
遠場(chǎng)渦流檢測采用較低的頻率(典型為50~500Hz),磁場(chǎng)穿過(guò)鐵磁性材料管壁,不受管壁厚度影響。
常規渦流檢測頻率較高(千赫范圍),受趨膚效應制約,磁場(chǎng)被限制在管壁有限厚度內,檢測厚壁列管外部缺陷較為困難。
3 渦流檢測技術(shù)特點(diǎn)
3.1 渦流技術(shù)在換熱列管檢測應用中的優(yōu)越性
1)非接觸式無(wú)損檢測,是檢測在役換熱列管的最行之有效手段。
2)檢測速度快,靈敏度高。
3)檢測信號為電信號,可進(jìn)行數字化處理,便于存儲、再現及進(jìn)行數據比較和處理。
4)渦流探傷時(shí),通過(guò)對檢測信號的相位-幅值分析,可就缺陷信號所表征的缺陷性質(zhì)、類(lèi)型、大小進(jìn)行有效判定。
5)渦流測厚時(shí),可實(shí)時(shí)顯示換熱列管全長(cháng)的壁厚分布狀況,并自動(dòng)記錄最薄截面的壁厚數據為檢測值,測量誤差在±0.05mm內。
3.2 渦流技術(shù)在換熱列管檢測應用中的局限性
1)需要制作專(zhuān)門(mén)的對比樣管進(jìn)行檢測基準的校準。
2)受渦流所特有的末端效應的影響,離換熱管口一定范圍內檢測信號將嚴重畸變,無(wú)法正確識別出缺陷,一般稱(chēng)此部位為渦流檢測的“盲區”。
3)對于U型管,由于探頭自身的長(cháng)度與剛性原因,無(wú)法穿入U型彎管的中心較小彎曲半徑段,故此區域管段無(wú)法進(jìn)行渦流檢測。
4)渦流檢測信號只表征換熱列管母材自身的變化狀況,無(wú)法反映出管子-管板角焊縫的狀態(tài),不能用于查找角焊縫的相關(guān)缺陷。
5)采用內穿過(guò)式線(xiàn)圈時(shí),對缺陷所處圓周上的具體位置無(wú)法判定;采用旋轉探頭式檢測雖可定位,但檢測速度慢。
4 渦流檢測系統組成
渦流檢測系統由檢測主機、數據分析系統、檢測傳感器(探頭)及對比樣管組成。
4.1 檢測主機(以ET556H為例)
用阻抗平面顯示,能實(shí)時(shí)得到缺陷信號的李薩育圖形,全面反映檢測信號的幅值、相位。
利用相位分析技術(shù),可將干擾與缺陷信號分開(kāi),提高信噪比。
激勵頻率范圍寬廣可調(50Hz~1MHz),相位3600可調范圍。
采用自動(dòng)平衡技術(shù)。
具備多頻檢測功能,可以有效抑制干擾
4.2 數據分析系統
利用計算機進(jìn)行檢測信號處理,具備混頻、報警設定、相位-幅值分析、數值存儲記錄等適時(shí)數據自動(dòng)分析處理功能。
采用專(zhuān)門(mén)開(kāi)發(fā)設計的檢測軟件,可自動(dòng)完成換熱列管壁厚的求平均值、分類(lèi)、統計等工作,并生成各類(lèi)直觀(guān)的數據分布圖;通過(guò)對分布圖的分析,可以了解設備管子的壁厚分布情況和腐蝕情況,從而分析引起腐蝕的設備和工藝因素。
4.3 檢測傳感器
渦流探傷時(shí),采用自比較式差動(dòng)線(xiàn)圈;渦流測厚時(shí),采用絕對式線(xiàn)圈。
一般情況下采用普通內穿過(guò)式,特殊情況下采用內壁旋轉探頭式。
4.4 對比樣管
用來(lái)校驗儀器檢測參數,保證檢測模型的精確性。
通常采用與被檢測換熱器列管相同材料及規格的管段進(jìn)行加工,特殊情況下可代用,但必須由具有豐富檢測經(jīng)驗的技術(shù)人員依據理論計算值進(jìn)行檢測偏差調整。
對比樣管按相關(guān)標準規定結構形式,根據具體檢測要求進(jìn)行設計;采用數控、線(xiàn)切割等高精尖加工手段,控制加工誤差滿(mǎn)足相關(guān)標準的規定。
檢測使用的對比樣管,必須能準確模擬被檢換熱列管的各種可能缺陷、壁厚減薄范圍。
5 在役換熱器列管渦流檢測的目的及內容
5.1 檢測目的
對在役換熱器的換熱列管進(jìn)行渦流檢測,實(shí)現一下檢測目的:
1)可估價(jià)換熱列管的全面工作狀態(tài),并通過(guò)常規檢查來(lái)評價(jià)某種狀態(tài)可能進(jìn)一步惡化的情況。
2)定量評價(jià)由于水或溶液的化學(xué)成分和設備運行情況的變化而使換熱列管產(chǎn)生變化的狀態(tài)、變化的速率以及設備的腐蝕速率,推算換熱器列管的剩余壽命。
3)研究整個(gè)換熱器換熱列管的缺陷和腐蝕的分布狀態(tài),以幫助分析并確定引起換熱器的狀態(tài)惡化及泄漏的原因。
4)為確定是否需要修理和進(jìn)一步在適當的時(shí)候換管提供有用的資料。
5.2 檢測內容
1)渦流探傷:檢測換熱列管是否存在裂紋、蝕坑、機械損傷等缺陷,評定缺陷的類(lèi)型、大小及性質(zhì)。
2)渦流測厚:檢測換熱列管全長(cháng)的壁厚變化狀態(tài),準確查找出最薄截面位置并確定殘余壁厚值,判斷列管壁的腐蝕狀態(tài)、腐蝕程度。
3)綜合以上兩項檢測內容,可準確判斷本次檢測時(shí)是否存在需要報廢處置的部件或設備,并預判在下一運行周期內換熱列管可能的腐蝕發(fā)展或是否可能出現泄漏,為換熱器安全運行提供可靠依據。
6 在役換熱器列管渦流檢測的實(shí)施要點(diǎn)
6.1 檢測方案的制訂
不同工藝介質(zhì)及運行特點(diǎn)、不同換熱列管材質(zhì)及壁厚的換熱器,其主要腐蝕特征及損壞形式均不相同。
因此,必須根據設備結構特點(diǎn)及工藝運行狀況、換熱列管材質(zhì)及壁厚、換熱列管表面狀態(tài)等因素,結合相應的檢驗標準或規范,綜合制訂檢測方案。
在檢測方案中,需規定:檢測主要目的、檢測系統、檢測參數、檢測程序、檢測評判標準及檢測報告形式。
6.2 對比樣管的標定
對比樣管的標定信號為現場(chǎng)檢測信號分析處理的基本依據。
檢測前,必須先通過(guò)檢測頻率、相位、增益等參數的設定,將對樣管進(jìn)行標定,獲得最佳檢測信號,以建立有效的檢測數據模型。
6.3干擾的抑制
由于換熱列管周?chē)泄馨搴椭伟瀛h(huán)繞,將會(huì )對檢測造成一定干擾。如果列管上恰在此部位存在缺陷,則干擾信號將會(huì )與缺陷信號疊加形成復合信號而難于判別,有時(shí)甚至會(huì )淹沒(méi)缺陷信號,因此必須抑制干擾。
常用的有效方法是采用混頻技術(shù)。
6.4 渦流探傷缺陷的評定
對檢測發(fā)現的缺陷信號進(jìn)行評定是渦流探傷最關(guān)鍵的技術(shù),尤其對多信號疊加形成的復合信號更難于分辨。
這就要求技術(shù)人員有豐富的檢測經(jīng)驗和對所測設備的充分了解,
在實(shí)際檢測中,常規渦流由于存在集膚效應及深度方向的相位滯后,因此用對比試樣對檢測系統進(jìn)行合適的調試后,依據缺陷信號的相位及幅度大小,可明確地區分缺陷的位置及深度,即缺陷是否穿透,是位于管子的內壁還是外壁及其大小等。
遠場(chǎng)渦流檢測技術(shù)由于不存在常規渦流檢測的集膚效應及深度方向的明顯相位滯后,因此通過(guò)相位變化來(lái)區別缺陷位于換熱管的內壁或外壁較為困難,也不能準確確定缺陷深度;只能通過(guò)實(shí)際檢測信號與模擬缺陷信號在相位和幅值上的差異,分析缺陷造成的金屬損失體積量,從而 “當量”評判缺陷程度。
由于遠場(chǎng)渦流場(chǎng)分布的特點(diǎn),即使換熱管上體積損傷量相同的缺陷,由于在分布方向和表現類(lèi)型上的不同,也會(huì )影響缺陷的檢出和判定。
若換熱管上缺陷相當接近其鐵磁性材料制作的支撐板,則受場(chǎng)效應的影響,支撐板信號將嚴重干擾實(shí)際缺陷信號,造成實(shí)際缺陷的有效檢出及正確識別相當困難。與此類(lèi)似,管束邊緣的換熱管,其缺陷信號也容易受到設備筒體上鐵磁性結構件的信號干擾。
遠場(chǎng)渦流檢測時(shí),對換熱管軸向裂紋的漏檢可能性比較大。這是由于激勵線(xiàn)圈產(chǎn)生的電磁場(chǎng)沿換熱管軸向平行傳播,對于換熱管軸向裂紋,一方面其總的金屬體積損失量較小,另一方面缺陷切割場(chǎng)流較小,在探頭上激勵的相對電壓變化較低,測量線(xiàn)圈接收信號不大明顯。
6.5 渦流測厚數據分析
渦流測厚時(shí),事先在軟件內輸入換熱器管板圖文件,按一定次序逐根檢測,數據分析系統直接讀取渦流信號并顯示為測厚曲線(xiàn),同時(shí)轉換成壁厚數值并實(shí)時(shí)對應顯示、存儲。
渦流測厚軟件所記錄的壁厚數值,為此列管的最薄截面的壁厚平均值;同時(shí),在檢測過(guò)程中依據測厚曲線(xiàn)的變化,可分析列管全長(cháng)的壁厚變化趨勢。
受現場(chǎng)環(huán)境因素的影響,渦流測厚曲線(xiàn)有時(shí)會(huì )發(fā)生漂移,從而導致檢測誤差的存在。這就要求檢測人員能迅速判斷出此誤差并及時(shí)采取措施糾正測厚曲線(xiàn)的漂移,以保證檢測模型的穩定性
7渦流檢測技術(shù)在合成氨裝置在役換熱列管中的工程應用實(shí)例
7.1檢測工程業(yè)績(jì)簡(jiǎn)介
作為國內最早在石化行業(yè)進(jìn)行在役換熱列管渦流檢測工程應用的檢測單位之一,重慶奧林特機電技術(shù)有限公司運用常規和遠場(chǎng)渦流檢測技術(shù),在全國范圍的不同領(lǐng)域進(jìn)行了大量的渦流檢測工程實(shí)踐;尤其是在具有較大技術(shù)難度的鐵磁性材料換熱列管遠場(chǎng)渦流檢測方面,積累了豐富的經(jīng)驗。
公司在換熱列管渦流檢測方面所服務(wù)的領(lǐng)域包括石油、石油化工、化肥、甲醇及其他各不同類(lèi)型化工裝置,服務(wù)廠(chǎng)家包括國外獨資、中外合資、大型國企等中外知名企業(yè),并與中石油、中石化、巴斯夫、BP等世界性大公司形成了長(cháng)期合作伙伴關(guān)系。
檢測換熱器近200臺次/年,檢測的換熱列管材料包括純奧氏體不銹鋼、銅合金、純鈦及鈦合金、純鎳及鎳基合金、哈氏合金、鋯-不銹鋼復合金屬等非鐵磁性材料和碳鋼、鉻鉬鋼、鐵素體-奧氏體雙相不銹鋼等鐵磁性材料,涉及的換熱管形式有直管、U型管、翅片管,換熱器型式有固定管板式、浮頭式、U型管式。
在合成氨生產(chǎn)裝置中,我們已經(jīng)成功地對以下在役換熱器列管進(jìn)行了多次渦流檢測:
第一廢熱鍋爐、第二廢熱鍋爐、合成再沸器、冷卻水處理器、碳酸鉀溶液再沸器、碳酸鉀溶液輔助再沸器、分子篩再生加熱器、再生塔再沸器、原料氣及循環(huán)氣一段氨冷器、原料氣及循環(huán)氣二段氨冷器、原料氣及循環(huán)氣三段氨冷器、氨合成塔進(jìn)氣原料氣換熱器、氨合成塔進(jìn)氣出氣換熱器、氨合成塔出口鍋爐給水換熱器、惰性氣洗滌器、冷水加熱器、合成氣水冷器、氨壓機出口氨冷器、氨合成塔底部換熱器、水煤氣換熱器、低壓廢熱鍋爐等。
7.2檢測應用實(shí)例
1)常規渦流探傷:
以某廠(chǎng)合成再沸器(105CB)檢測為實(shí)例。
該換熱器為浮頭式,換熱列管材料為SA249 TP316SS型不銹鋼,規格¢19.05×1.65×4000,共2400根,其中檢測前已堵管22根。
換熱器管程介質(zhì)為MDE溶液,殼程介質(zhì)為變換氣(氮氣、氫氣)。
檢測時(shí),采用ET-556型數字多頻渦流儀,對比樣管為T(mén)P316L型不銹鋼,規格¢19.05×2.11 孔型,檢測傳感器為高頻差動(dòng)內穿過(guò)式,人工拉動(dòng)探頭。
經(jīng)參數調節后,獲得對比試樣管上人工模擬缺陷檢測信號阻抗圖類(lèi)圖3,并據此建立缺陷信號深度-相位曲線(xiàn)圖類(lèi)圖4。
實(shí)際檢測結果為:12根列管存在可計性缺陷信號,其中A級缺陷8根,D級缺陷4根。
其中:管號為55-26的列管,于離下管口約1.5米附近,獲得缺陷信號阻抗圖如圖6。
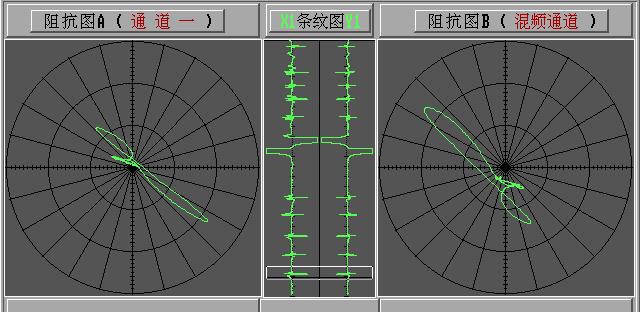
圖6 合成再沸器列管55-26渦流探傷信號
檢測判定該缺陷級別為D級,具備穿透性;抽出列管后證實(shí)檢測判定無(wú)誤(見(jiàn)圖7)。
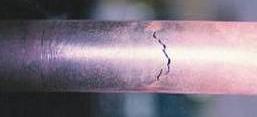
圖7 合成再沸器列管55-26穿透性裂紋
2)遠場(chǎng)渦流探傷:
以某廠(chǎng)合成氣廢熱鍋爐檢測為實(shí)例。
該換熱器為固定管板式,列管材料為16Mo3,規格¢30×2.5×5400,共876根。
管程介質(zhì)為工藝合成氣,殼程介質(zhì)為蒸汽。
檢測時(shí),采用ET-556型數字多頻遠場(chǎng)渦流儀,對比樣管為16Mo3 ¢30×2.5 模擬缺陷分布為通孔、平底孔、環(huán)槽、平槽,檢測傳感器為內穿過(guò)式,人工拉動(dòng)探頭。
經(jīng)參數調節后,獲得對比試樣管上人工模擬缺陷檢測信號阻抗圖如圖8~11。
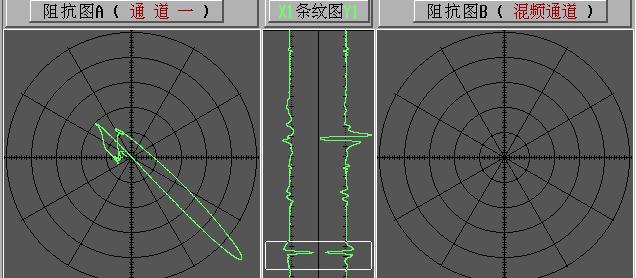
圖8 對比試樣上通孔信號
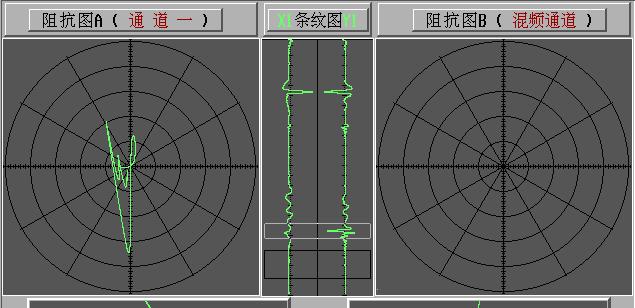
圖9 對比試樣上40%單邊銼槽信號
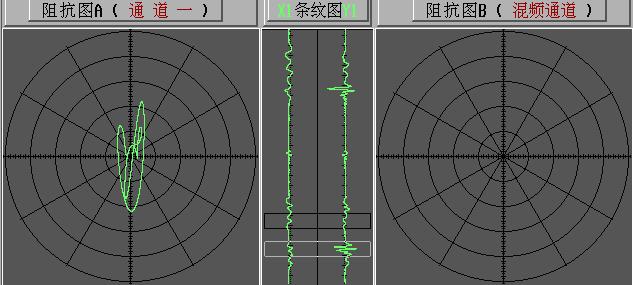
圖10 對比試樣上20%平底孔信號
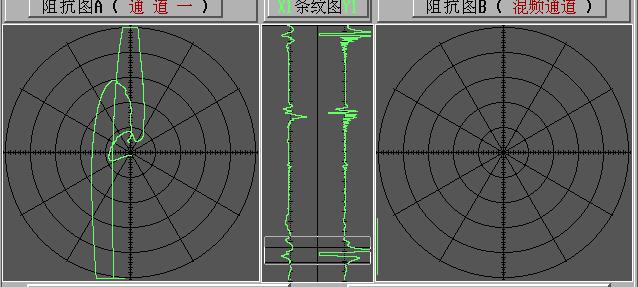
圖11 對比試樣上20%環(huán)槽信號
實(shí)際檢測結果為:25根列管存在可計性缺陷信號。
其中:管號為25-12的列管,于離下管口約1.2米處,獲得缺陷信號阻抗圖如圖12。
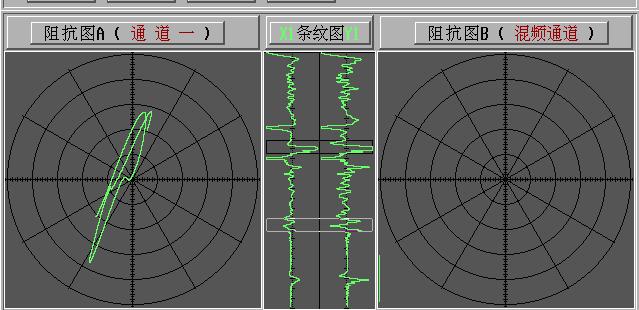
圖12 合成氣廢熱鍋爐列管25-12渦流探傷信號
可以看出:缺陷信號幅值接近于對比樣管上20%平底孔人工缺陷,但相位角大于20%環(huán)槽人工缺陷。
檢測判定該缺陷深度不到壁厚的20%,系外壁磨蝕造成的局部淺表缺陷。
3)渦流測厚:
仍以某廠(chǎng)合成氣廢熱鍋爐檢測為實(shí)例。
檢測時(shí),采用ET-556型數字多頻遠場(chǎng)渦流儀,對比樣管為16Mo3 ¢30×2.5 厚度為2.5/2.0/1.5,檢測傳感器為內穿過(guò)式,人工拉動(dòng)探頭。
檢測結果統計為:最大壁厚2.60 mm,最小壁厚2.05 mm,平均壁厚2.44 mm。
檢測獲得某列管測厚曲線(xiàn)如圖13。
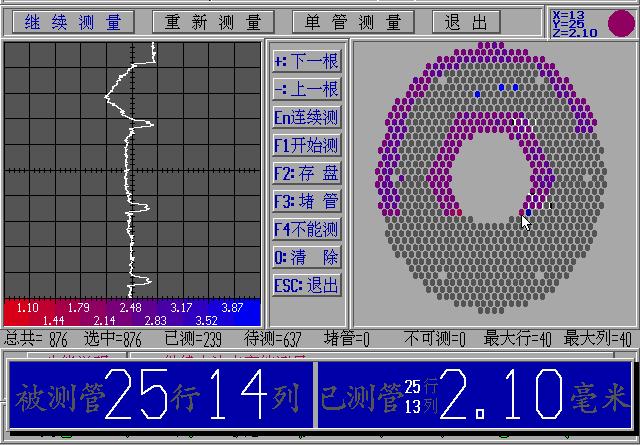
13 換熱列管渦流測厚曲線(xiàn)
儀器自動(dòng)記錄最薄截面平均值2.10mm為該列管壁厚測量值。
由圖13可以分析出:該列管存在明顯減薄區,減薄區位置在下管口往上600~1000mm范圍;與同一列管上其他壁厚均勻的管段部分相比,減薄值在0.3mm~0.35mm左右。
全部被檢列管的壁厚數據分布圖見(jiàn)圖14。
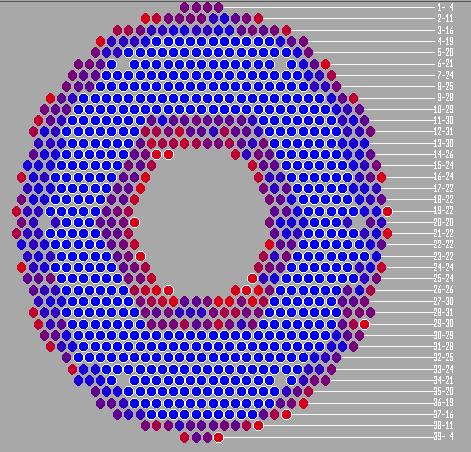
圖14 換熱列管渦流測厚數據分布管板圖
結束語(yǔ)
1)作為一種先進(jìn)的無(wú)損檢測技術(shù)手段,渦流檢測技術(shù)對在役換熱器換熱列管的檢測具有不可替代的應用前景。
2)多年的檢測經(jīng)驗表明:有計劃地對重要設備進(jìn)行定期檢測,能夠預先發(fā)現潛在的缺陷,掌握設備的實(shí)際腐蝕狀況并預測其殘余壽命。